Illinois OSHA Citations
They’re rampant, they hide in plain sight, and they have potentially dire consequences for your people and your bottom line. Is your dealership doing enough to avoid the most common OSHA citations in Illinois?
Although many people think of OSHA as a monolithic federal agency, it actually operates as a network of regional offices, each with its own priorities and enforcement strategies.
On the state level, OSHA’s actions are guided not only by nationwide concerns such as the top 5 citations but also by what the agency calls Local Emphasis Programs (or “LEPs” for short) and Regional Emphasis Programs. According to OSHA, these programs are “intended to address hazards or industries that pose a particular risk to workers in the office’s jurisdiction.” i
This means that dealers need to pay careful attention to your local OSHA office and its particular health and safety directives. Stay ahead of inspectors – and ensure the safety and health of your dealership’s workforce – by controlling the unique risks present in any local environment in which you do business.
Workforce Health and Safety Issues for Dealers in Illinois
Illinois is located in OSHA Region 5, headquartered in Chicago. Here are a few health and safety issues OSHA focuses on in Region 5:
Slips, Trips, and Falls
Fall protection is a nationwide workplace health and safety concern, but it’s a particularly pressing issue in Illinois given the state’s climate and concentration of industrial activity.
Common causes of fall violations include:
- Wet surfaces
- Uneven surfaces
- Inadequate lighting
- Ladders that have been improperly set up
- Ladders with structural defects
- Crowded workspaces
- Dangerous weather conditions, e.g. snow and wind
- Human error
- Poor fall protection precautions
- Inadequate training
To protect workers from falls, dealerships must do things such as the following:
- Eliminate any known dangers in the workplace
- Keep floors as clean and dry as possible
- Cover floor holes workers can fall into
- Provide guardrails and toe-boards around open-sided platforms, floors, and runways as soon as possible.
- When required, provide other means of fall protection, including safety harnesses, nets, and railings
- Provide workers with personal protective equipment at no cost to them
- Train workers about fall hazards
Additionally, to minimize fall risk and identify potential hazards, consider the following questions:
- Have you found and eliminated all fall risks? Walking surfaces and ladders should be kept clean and dry at all times. Holes should be covered. Equipment should be installed and used correctly. A competent member of your staff should regularly assess each facility for fall hazards. Once a hazard has been identified, it should be addressed as soon as possible. Walk-throughs should be conducted daily. Fall prevention, restraint, and arrest equipment should be inspected before each use.
- Are you using passive engineering controls and fall restraint systems when necessary? If you can’t eliminate a fall risk, you need to ensure warning signage in place, and planned passive engineering controls (such as guardrails) are ready. Use a fall restraint system when your employees are working near an unprotected edge or side. This kind of system typically requires a body harness and lanyard attached to an anchor point.
- Do you have fall arrest systems ready? If you can’t prevent or mitigate fall risk, you need to have fall arrest systems in place. Fall arrest equipment is designed to withstand the force of a fall by controlling it and preventing the worker from hitting a hard surface. A personal fall arrest system must use an anchor point able to withstand a downward force of 5,000 lbs. Otherwise, it must be supervised by a qualified person who has designed the system’s ability to arrest a fall’s downward force by a safety factor of 2. The PFAS must limit maximum arrest force – the most force that the person attached to the system will experience – to 1,800 lbs.ii
- Are you training workers on fall protection? Any worker who could be exposed to a fall hazard must receive training before they start working in an elevated area. The training should explain your fall protection policies and systems, how to select and use protective devices, and how to maintain equipment. Employees should also be trained to understand the requirements and proper safety procedures for personal fall arrest systems.
Forklifts
Forklift violations are common in Illinois, as many businesses in the state depend on the vehicles to move heavy materials.
One of the leading causes of forklift-related injuries and OSHA citations is inadequate training. Make sure that all forklift operators in your facility are properly trained and certified before they get behind the wheel. Too often, forklift operators begin working before an experienced forklift certification specialist evaluates and signs off on their training.
Damaged and poorly maintained vehicles are behind countless safety incidents and violations.
Keep an eye on the condition of your forklifts. Damaged and poorly maintained vehicles are behind countless safety incidents and violations. Make sure all forklifts are inspected between shifts. It’s a good idea to use a checklist. Take any machine out of rotation if there are issues such as problems with the mast, a broken or missing seatbelt, an expired fire extinguisher (for forklifts that must be equipped with one), rusted lifting chains, worn tires, and so forth.
Safe Driving
Vehicle accidents are a common workforce safety issue for dealers. Collisions can cause severe injuries as well as damage to property and equipment – and, of course, result in OSHA fines.
Fortunately, most accidents are avoidable. To improve safe driving habits and reduce the chance of an accident, employers should do the following:
- Practice good housekeeping and recordkeeping. For many dealerships, accidents frequently occur at one or a handful of problem areas. Maybe there’s a busy intersection on the lot or an obstruction at a corner creating a large blind spot. Look for and eliminate potential hazards proactively, and address issues as soon as there’s an incident. Employees are sometimes aware of these problems before health and safety managers are, so encourage the members of your workforce to speak up if they’ve witnessed an accident or noticed a hazard.
- Be mindful of where vehicles are parked. Drivers should respect all signs and markers, and never leave a vehicle in a spot where it shouldn’t be parked – regardless of how quickly they intend to return. An improperly parked vehicle can increase the likelihood of collisions, as other drivers don’t expect the vehicle to be there or can’t see it, and may cause serious problems if there’s an emergency, e.g., if the vehicle is obstructing a fire lane.
- Look out for speeding and distracted driving. Drivers should obey speed limit signs (make sure to post these if you haven’t already), watch out for pedestrians, and never use a mobile device, fill out paperwork, or engage in other activities besides operating the vehicle while in the driver’s seat. Discourage multitasking. No accident is worth a couple minutes saved.
Examples of indirect workplace hazards expenses
- Workers’ compensation claims from people who have experienced injuries and illnesses
- Lost productivity during and after an incident
- Lowered workforce morale due to fear and uncertainty around risk areas
- Hours of labor spent identifying and fixing the issue
- Expenses of cleaning and replacing equipment that’s out-of-date, damaged or broken
- Legal and compliance fees
- Negative publicity and reputational damage
Staying Up-to-Date on Regulations, Reporting, and Training
Don’t wait until OSHA comes knocking to make sure your EHS paperwork, policies, and training are complete and up to date. Investigators pay attention to everything, and the seemingly tiniest details can lead to violations. For example, if the last three months of inspection forms have been filled out in the same handwriting with the same color of ink, that’s a dead giveaway to OSHA that the employer may be falsifying information.
Stay compliant and keep your workforce safe by recording and reporting everything on time, providing periodic refresher training to employees, and keeping your policies in line with all regulatory updates. Automated safety and compliance software makes this easy.
The Cost of an OSHA Violation
OSHA penalties can exceed $13,000 per violation and as much per day for every day the issue hasn’t been fixed by OSHA’s deadline. The fine for a willful or repeated violation can be 10 times as much. In 2021, the maximum penalty for such a violation is $136,532.iii
Those are just the direct costs. Organizations that don’t adequately address common workplace hazards can expect to pay hundreds of thousands – even millions – in indirect expenses.
Of course, the true costs of a safety violation are incalculable. No one can put a number on an employee’s life. Suffice it to say, it’s in your organization’s best interest to bring your annual number of injuries and illnesses to zero.
Fortunately, avoiding an OSHA citation isn’t as complex or cost-intensive as many people think. Small steps can save you six or seven figures – or save someone’s life.
Read on to learn about the five most common OSHA violations and what you can do today to reduce their chances of happening in your workplace.
Top OSHA Citations Across the U.S.
Here are the top OSHA citations across the country in 2020. This list has remained largely unchanged for a decade. The reality is undeniable: many environmental, safety and health professionals are failing to adequately recognize and mitigate the greatest sources of workforce risk.
No matter how much you know (or think you know) about the most common workplace violations out there, it’s clear that organizations could use some help.
In fiscal year 2020, OSHA issued hundreds of citations combined in the following categories:iv
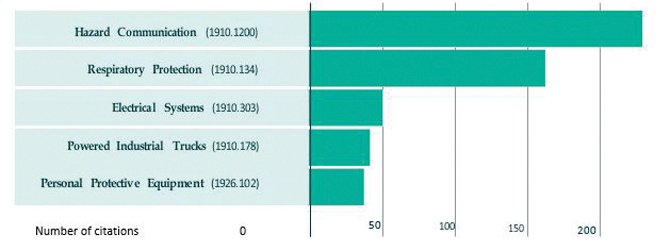
You Don’t Have to Manage Your OSHA Requirements Alone
Have questions? Looking for more detailed OSHA compliance guidance? KPA is here to help.
This is only a basic overview of the most common violations in Illinois. To truly protect your workforce and bottom line, you’ll need in-depth information – and not just about these key areas, but every potential hazard that exists in your dealership. You’ll also need to conduct a thorough evaluation of your facilities to identify current gaps and risk areas.
KPA’s unique combination of expert EHS consulting services, software, and training can provide the coverage your people and your dealership needs.
KPA clients get access to more than 120 field consultants across North America who are available to deliver both on-site and virtual compliance support, as well as audit loss control services. Additionally, KPA’s Vera Suite software helps dealers manage their EHS, F&I, and HR programs in one comprehensive platform.
The combination of KPA’s software platform and deep industry expertise helps clients manage risk, streamline operations, and reduce costs.
i https://www.osha.gov/enforcement/directives/lep
ii Full requirements can be found at https://www.osha.gov/dts/osta/otm/otm_v/otm_v_4.html#fall_arrest
iii https://www.osha.gov/penalties
iv Motor Vehicle Parts and Dealers Data Auto Repair and Maintenance Data